Case Studies: Real-World Success Stories
How Annual Leak Detection Services Support Municipal Capital Planning
Yearly water leak detection services can play a critical role in helping municipalities develop and maintain effective capital improvement plans
Benefits of Reducing NRW for Municipalities
1. Financial Savings & Revenue Recovery 2. Improved Infrastructure Performance 3. Environmental Sustainability 4. Public Trust & Service Reliability 5.
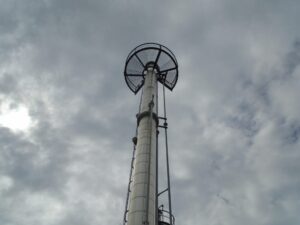
Stray Gas Leak Detection
Challenge Air monitor alarms continued to be triggered in a process building, indicating dangerously-high concentrations of H2S. Numerous attempts to
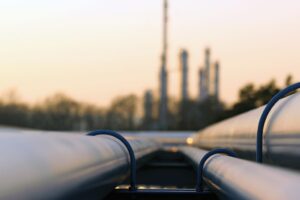
Multiple Pipeline Leak – FlowTRACE
Challenge A sump tank located at a facility had multiple underground inlet lines. A leak surfaced on location and the
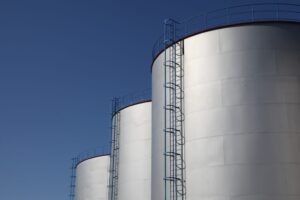
Large Diameter Tank Leak – FlowTRACE
Challenge A 135-foot wide and 51-foot tall tank had fluid leaking from its base. Constraints The tank was imperative to
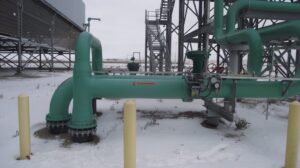
Power Plant Leak – FlowTRACE
Challenge: A closed-loop glycol cooling system inside a power plant was losing 4.5L of coolant per hour. We needed to
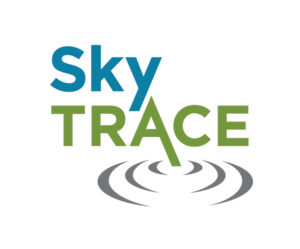
The SkyTRACE Solution for Major Pipeline Leak Detection
EnviroTRACE, a pioneering environmental company specializing in sensitive leak testing services, was subcontracted by a prime contractor for a significant